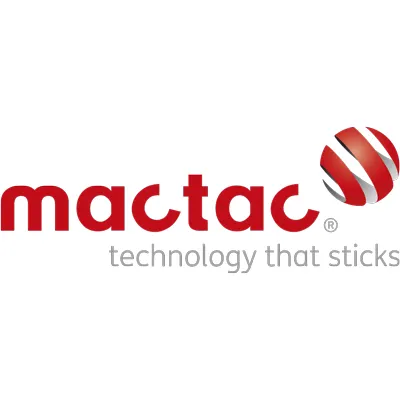
PermaFlex®PRODUCT: IP6200 5 Mil Lustex® PERMACOLOR® The PermaFlex® overlaminating films is a family of relatively thick films that are coated with pressure sensitive adhesive on one side. These unique films can be laminated to either one or both sides of photographic prints, transparencies and digital images (inkjet, electrostatic, and thermal) to impart protection, surface texture and enough rigidity to eliminate the need for mounting to traditional flat substrates in many applications.
You Must be Logged in to Add the Item to your Cart.
Description
PermaFlex® PRODUCT: 5 Mil IP6200 Lustex® 5
PERMACOLOR®
The Permacolor system is a series of pressure sensitive products for mounting and overlaminating in the imaging industries. Pressure sensitive Permacolor provides fast, efficient processing through cold roll lamination techniques without the need for heat, drying or messy coating operations.
These PermaFlex® overlaminating films is a family of relatively thick laminating films that are coated with
pressure sensitive adhesive on one side. These unique films can be laminated to either one or both sides of
photographic prints, transparencies and digital images (inkjet, electrostatic, and thermal) to impart protection, surface
texture and enough rigidity to eliminate the need for mounting to traditional flat substrates in many applications. These
laminates also retain enough flexibility to allow images to be used in non-flat configurations such as on cylindrical
displays. This feature also permits the laminated images to be rolled for easy shipping or storage. IP6200 is a 5-mil film with a special “Lustex®” surface. The low gloss texture helps eliminate glare and provides a very unique and pleasing viewing surface. This product can be used as an overlaminate for indoor as well as outdoor applications. IP6200 not only provides protection from abrasion and moisture, it also helps retard color fade caused by ultra violet (UV) light exposure.
IP6200 can be used for interior Floor Graphics as it exceeds industry standards for slip resistance, when tested
according to ASTM D2047.
TYPICAL VALUES*
PHYSICAL PROPERTIES TEST METHOD
Thickness, inches (μm) ASTM-D645
Film plus adhesive 0.0065 (165)
Flame Resistance - Underwriters Laboratories Classified as to Surface Burning Characteristics
Flame Spread 10 UL - ANSI/UL-723
Smoke Developed 70 CAN/ULC - S102M
(control No. 2P72)
ANSI Class A
NFPA Class A
UCB Class I
White light Transmission, % 92 MACtac CTM-67
(Note: Glass = 100%)
Gloss (60° angle) 15 ASTM D-523
Static Coefficient of Friction (Slip Resistance) ASTM C 1028
OSHA recommendations: SGS US Testing Co.
Dry floors _ 0.5, Wet surfaces & Handicap accessible routes _0.6, Ramps _0.8
Dry Neolite 0.94
Wet Neolite 0.72
Temperature Range Guidelines
Application: Above 50°F (10°C) for best results.
End Use: -20° to 200°F (-29° to 93°C)
Adhesive pH Neutral TAPPI-529
Direct Food Contact FDA conditions of Use B through H 21 CFR 177.1580
Subsections (a), (b) & (c)
Co-efficient of Expansion 1.7 X10-5 in/in/°C ASTM D696
IMPORTANT NOTICE: The information given and the recommendations made herein are based on our research and are believed to be accurate, but no
guarantee of their accuracy or completeness is made. In every case, user shall determine before using any product in full scale production, or in any way, whether such product is suitable for user’s intended use for their particular purpose under their own operating conditions. User assumes all risk and liability
whatsoever in connection with their use of any product. The products discussed herein are sold without any warranty as to merchantability or fitness for a particular purpose, or any other warranty, express or implied. No representative of ours has any authority to waive or change the foregoing provisions, and
no statement or recommendation not contained herein shall have any force of effect unless in an agreement signed by the officers of seller and manufacturer. Nothing contained herein shall be construed to imply the nonexistence of any relevant patents or to constitute a permission, inducement or recommendation to practice any invention covered by any patent without authority from the owner of the patent. The following is made in lieu of all warranties, express or implied: Seller’s and manufacturer’s only obligation shall be to replace or credit such quantity of the product proved to be defective at its discretion.
TM Trademark of Morgan Adhesives Company.
® Registered Trademark of Morgan Adhesives Company.
www.MACtac.com
DURABILITY:
The durability of the film is 2-3 years in vertical (90±5°) applications outdoors and 5+ years indoors in vertical
applications and two years for interior Floor Graphics. While all Permacolor overlaminating films have UV resistance built in to help extend the life of your image, the durability of the image is mainly dependent upon the quality of the inks (see technical data sheets given by the ink manufacturers) and pressure sensitive media being used.
SHELF LIFE
Two years when stored at 75°F (24°C) and 50% relative humidity or less. Note: MACtac recommends that rolls be
stored on end or suspended from the core.
RECOMMENDATIONS FOR ROLLING AND SHIPPING LAMINATED IMAGES:
MACtac studies and field surveys with numerous customers using Permacolor® laminates in rolled-up graphic
applications, leads to the following recommendations for rolling and shipping laminated images:
1. Prior to rolling graphics:
a) A 2 - 4 hour wet-out period is strongly recommended for the adhesive system to build to ultimate adhesion. This will significantly improve your success with rolled-up graphics.
b) This product can be used over UV inkjet and screen printed images. However, extra wet-out time is required to reduce silvering and build bond prior to rolling.
2. For single-side laminated images:
a) Roll laminated side out for shipping and storage.
b) An inside roll diameter of 3 - 5 inches, minimum, is recommended for graphics with less than 10 mil
total graphic thickness (includes imaged media and Permacolor overlaminates).
c) For images with a total thickness of 10 mils or greater an inside roll diameter of 10 - 12 inches,
minimum, is recommended.
3. For images laminated on both front and back sides:
a) Roll images with the thicker laminate to the outside for shipping and storage. For example: if your
image has 5 or 10 mil polycarbonate on the front and 15 mil polycarbonate on the back (for additional
stiffness), roll the graphic with the 15 mil PermaFlex® side out.
b) All double laminated images should be rolled with an inside roll diameter of 10 - 12 inches minimum.
Remember that a larger inside diameter is better.
Please keep in mind that this is a recommendation, individual experience should not be discounted. We
recognize that different laminators and laminating methods may produce different results. The recommendations above represent our experience as having the “greatest” success in the field.
1) The user is responsible for determining the product’s suitability, including adhesion and if needed, removal characteristics when used in applications other than listed specifically in this Performance Guide.
2) If there are any questions about applications, please contact your MACtac sales representative to discuss your requirements for recommendations.
3) If this is a printed Performance Guide it is an uncontrolled document. Please check the GRS website for the latest, most up-to-date version.
* Values given are typical and are not necessarily for use in specification.
CALL 1-888-477-8465 for additional product information